|
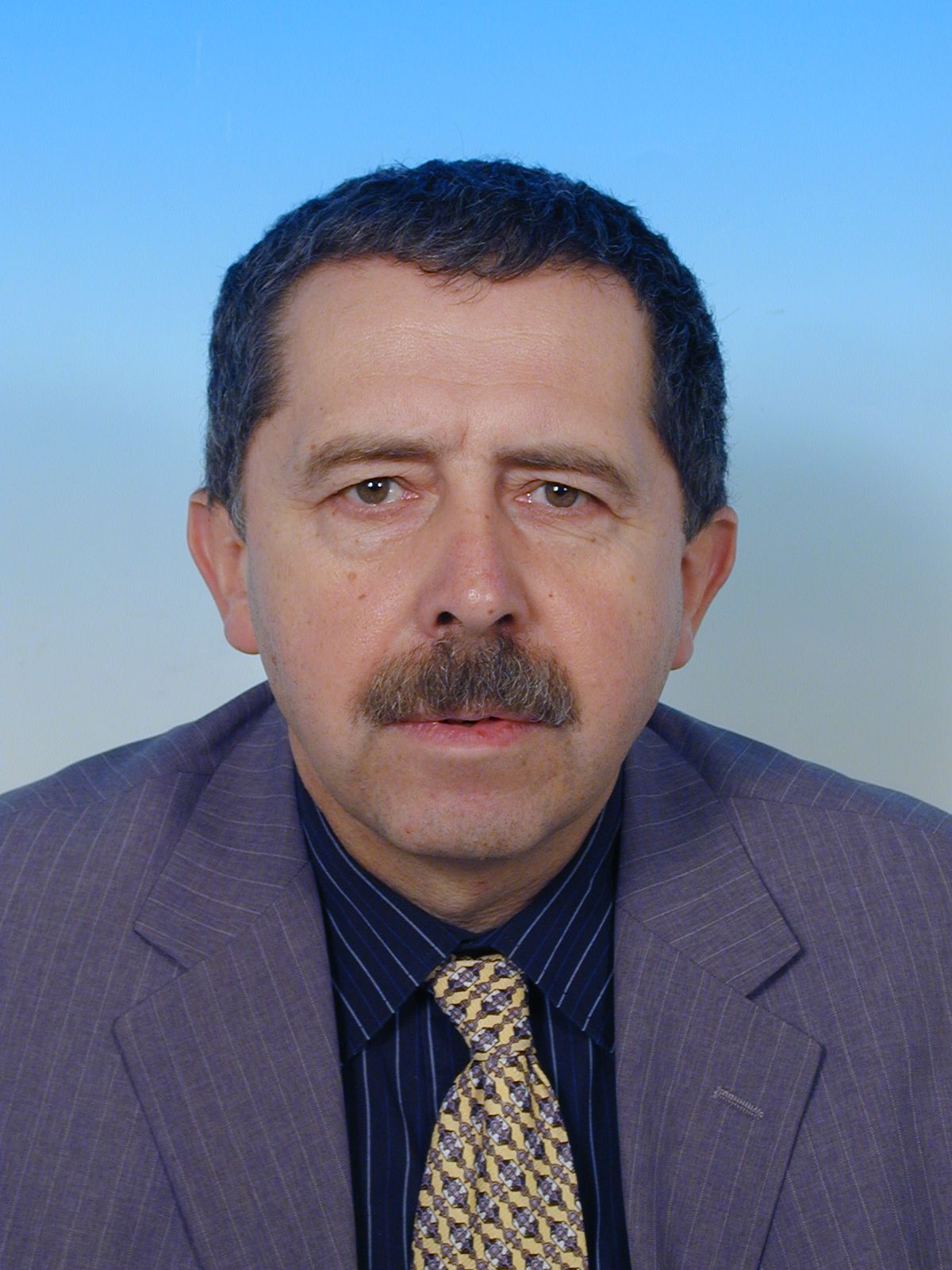 |
Jiri Sloupensky
Rieter CZ s.r.o., Usti nad Orlici
Czech republic |
|
Title: Novel sensors in Rieter CZ s.r.o.
Abstract: With the rising of living standards of the population after World War II there was also increased demands for textile products, especially clothes. The limiting factor for that was the insufficient capacity in the production of yarns, which is the basic raw material for production of flat textile products, namely woven and knitted fabrics. In several countries, including the former Czechoslovakia, there were initiated programs to increase productivity in cotton mills. In addition to the improving of conventional technologies there were investigated the possibilities of unconventional manufacturing technologies. A great achievement was the invention of the so-called. OE technology in cotton research institute in Ústí nad Orlicí in 1965. This technology was subsequently extended to the whole world through licenses, sold to the leading manufacturers of textile machinery. Due to the high productivity of such a machines it was necessary to use sensors that monitor the spinning process and in case of a failure the production was stopped.
Large-scale development of this new technology, along with the development of the classical spinning, was able to secure the needs of the population in the area of textiles so that we are not talking about any deficiencies any more. Along with the availability of textile products and therefore rising demands on the quality there was also pressure to increase the quality of the yarn itself. Defects, that were previously acceptable, today may no longer appear in the final product. This trend has led gradually to equipment of individual spinning positions by electronic yarn sensors continuously measuring the produced yarn. In case of defect, the process is interrupted and the defect is removed. The lecture describes the different principles of these sensors based on capacitive and optical principles and their advantages and disadvantages. |
Bio: Jiri Sloupensky received his M.Sc. degree in Electronic Computer Engineering from the Czech Technical University, Prague. He then worked at the Cotton Industry Research Institute in Usti nad Orlici, developing microprocessor based control systems for advanced spinning machinery, based on Rotor spinning principle. This activity also formed the basis of his PhD work in Technical Cybernetics; he received his Ph.D. degree in 1986. Since 1991, he has been leading the Research and Development department of Rieter CZ in Usti nad Orlici, which is a subsidiary of the Swiss company Rieter. Since 2007 he holds position of Vice President Product Research. He contributes to the new designs for textile spinning machinery based on advanced mechatronic concepts. During his research carrier he applied more than 60 patents in the area of advanced sensor technology and other mechatronic solutions.
|
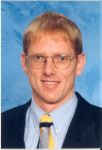 |
Elmar Schaefers
Siemens AG, Erlangen
Germany |
 |
Title: Model based control approaches for Machine tools
Abstract: From control theory we know that model based control algorithms do have the potential to significantly increase machine dynamics and accuracy. But, for the dynamic requirements of machine tools the classical model based approaches require a very good matching of model and reality what makes the modelling effort quite high. As a consequence, these approaches are not available based on industrial numeric controllers. This talk will deal with a new approach where dynamic machine models are solely used to adapt feedforward signals to mechanical resonances. The models can be kept quite simple and the benefit is high: Especially for machine tool applications where the excitation of resonances is mainly caused by the acceleration and deceleration forces this new approach results in a substantial increase of machine dynamics. Within the second part of this presentation a feedback control method is outlined allowing an active damping of mechanical resonances using servo motors of the feed axes. Applications with high process forces exciting mechanical eigenfrequencies may be restricted by a little damping of critical eigenmodes. Consequently, an active damping of these modes results in a productivity increase. |
Bio: Elmar Schäfers gained his doctorate in control engineering in 1998 at the university of Karlsruhe, institute of control systems. Since 1999 he works for research and development at Siemens motion control systems. From 2006 to 2014 he was head of a development department with the core areas mechatronics and predevelopment projects. Today he is key expert for Drive Train System / System Optimization. He holds numerous patents and was one of the Siemens inventors of the year in 2010. |
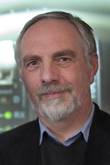 |
Heinrich T. Vierhaus
BTU Cottbus-Senftenberg
Germany |
 |
Title: Error Resilience in Digital Integrated Circuits
Abstract: For more than 10 years, many authors have predicted dependability problems with large-scale integrated circuits, implemented in nano-technologies. Reasons are new and enhanced fault mechanisms that affect either a higher vulnerability against transient faults, caused by particle radiation, or pre-mature aging due to device degradation. More recently, power dissipation on ICs has become a major problem, also affecting reliability aspects, since most fault mechanisms are strongly enhanced by higher temperatures. The final challenge is to handle a variety of fault effects at minimum cost in extra hardware in order to enhance dependability and system life time.
The tutorial first gives an introduction into the basic problems. Next methods for the detection and correction of short transient faults are shown. Then methods that can detect and correct delay faults are presented, followed by new architectures that may handle transient faults and delay faults in combination. Built-in self repair (BISR) is presented as a method that is not capable of on-line error correction, but may be helpful for life-time extension. Finally there is a comparison of such technologies in terms of requirements for extra time or extra power.
|
Bio: Heinrich Theodor Vierhaus received a diploma degree in electrical engineering from Ruhr-University Bochum (Germany) in 1975 and a doctorate in EE from the University of Siegen in 1983. From 1983 to 1996 he was a senior researcher with GMD, the German national research institute for information technology. Since 1996 he has been a full professor of computer engineering at Brandenburg University of Technology, since 2013 re-founded as BTU Cottbus-Senftenberg.
He has authored more than 100 papers in the area of test, testable design and fault tolerant computing, and he was the General Chair of the IEEE DDES 2011 symposium in Cottbus. He is also the coordinator of the East-Central European network on “Dependable Cyber Physical Systems”, linking 5 universities in 4 countries.
|
|